Наручные часы на газоразрядных индикаторах ИН-16
Оглавление:
Введение
Электроника и схемотехника
Печатная плата
Изготовление корпуса
Стекло, винты и ремешок
Станция зарядки и о дельта-принтерах
Облагораживание корпуса и ацетоновая баня
Конечная сборка
Заниматься изготовлением печатных плат, да и вообще электроникой, я начал именно для создания для таких наручных часов на газоразрядных индикаторах. Конечно, без должной подготовки в трассировке и производству этих плат такое не сделать. Дорожки на ПП всего лишь толщиной 0,3 мм, микроконтроллер мелкий. Плату можно заказать на производстве.
Идеей и вдохновением для создания такой вещи послужил аналогичный проект наручных часов известного в узких кругах Тимофея Носова. Мой проект имеет такие же индикаторы ИН-16 и компоновку корпуса, но все остальное я поменял для удобства разработки. К примеру, я применил обычную атмегу8 вместо PIC микроконтроллера, который был в оригинале. К тому же, AVR очень просты в программировании и прошиваются через обычный SPI интерфейс.
Электроника и схемотехника
В высоковольтный преобразователь влез я, поменяв силовой транзистор, потому что я не смог найти такой же. Как следствие, преобразователь не работал как надо. Симптомы таковы: как только аккумулятор начинал разряжаться, то напряжение на выходе резко падало и цифры горели лишь частями. Левая лампа ввиду каких-то особых причин зажигается при большем напряжении, и она вообще в таком режиме отказывалась работать.
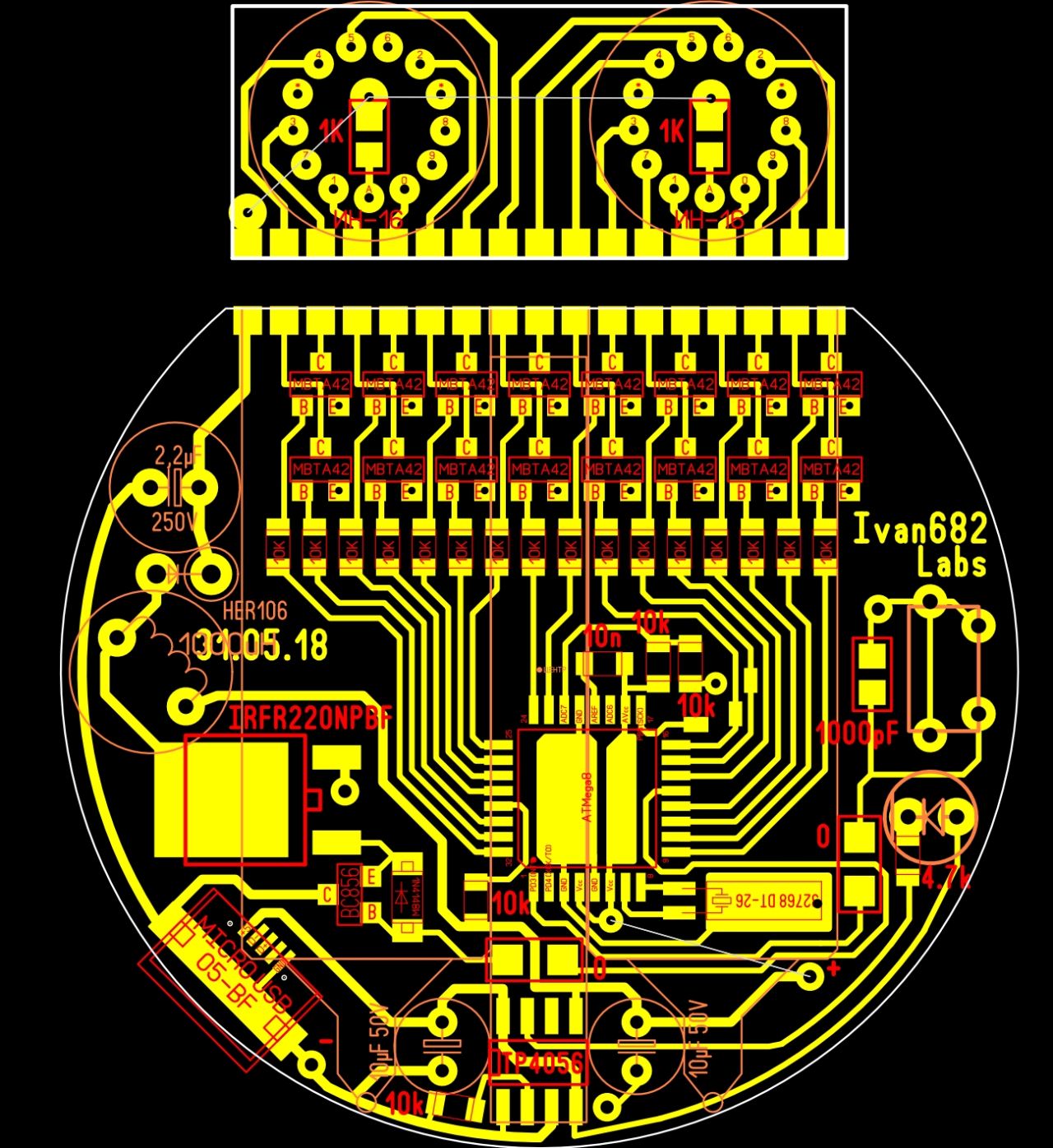
Сам преобразователь - это простейший повышающий DC-DC. У него четыре базовых элемента: силовой транзистор (ключ), катушка индуктивности, диод и конденсатор. На затвор полевого транзистора подается ШИМ-сигнал с микроконтроллера, который заставляет открываться/закрываться силовой транзистор. Ток через катушку замыкается на землю, когда транзистор открыт, а когда закрывается, то из-за запасенной в катушку энергии, происходит резкий всплеск напряжения и оно проходя через диод заряжает конденсатор. Этот процесс происходит постоянно, когда нужно высокое напряжение. Энергия накачивается в конденсатор и мы получаем высокое напряжение.
Я стал грешить на транзистор. Напряжения бортовой сети часов катастрофически низкие, значит в преобразователе будут серьезные токи, а чтобы эти токи были, нужно достаточно сильно открыть силовой транзистор. Вот тут-то и зарыта собака! Стало ясно - пока напряжение в сети достаточно для полного открытия транзистора, то преобразователь выдает нужное напряжение (почти) и индикаторы горят. Я подобрал транзистор с низким напряжением затвора для полного открытия, гораздо ниже минимального напряжения питания и проблема отпала. Осталась только разница в напряжении зажигании разных ламп. Проще говоря, нужно подбирать индикаторы по одинаковому напряжению зажиганию или хотя бы исключать сильный разброс (>10Вольт).
Печатная плата
Началось все с проектирования печатной платы. Как я писал выше, за основу была взята готовая плата часов, но из нее выкинута вся управляющая часть, упрощена светодиодная индикация часов и минут (убрана полностью), заменен силовой транзистор в преобразователе высокого напряжения, убраны часы реального времени за счет использования встроенного асинхронного таймера в микроконтроллере. Оставлена транзисторная коммутация катодов в текущей разводке, компоновка разъема зарядки и кнопки для совместимости с готовыми моделями корпусов.
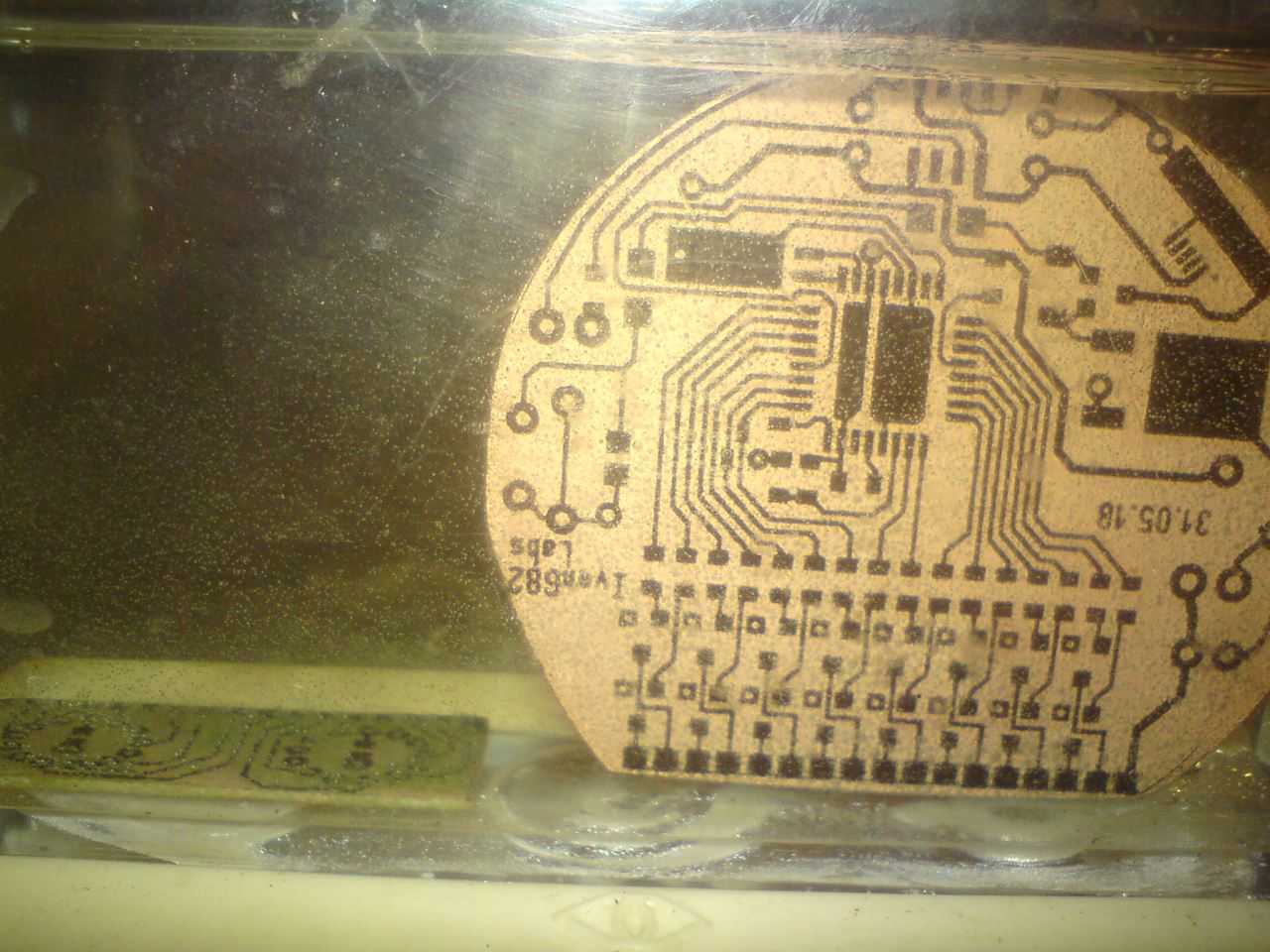
Я изготовил плату по привычной мне технологии, все тем же утюгом, все той же перекисью. Круглая плата вырезается также обычными ножницами по металлу, после пришлось подравнивать абразивным инструментом. В текущей трассировке печатной платы обратная сторона (лицевая) является цельным полигоном, это сделано для упрощения изготовления, так как отпадает необходимость переносить рисунок с двух сторон. В этом случае следует этот факт учитывать и нужно заклеить эту сторону обычным скотчем перед травлении.
После травления платы, нужно про зенкеровать отверстия с лицевой стороны, которые не соединяются с земляным полигоном. У ключей коммутации катодов земляной вывод соединяется с полигоном без каких либо дорожек. Это немного неправильно, и в следующей ревизии платы будет исправлено за счет применения двухсторонней трассировки. Эти перемычки, как и все остальные, изготовляются из жилок многожильного провода. Когда все перемычки запаяны, нужно проверить контакт мультиметром, чтобы потом не искать причину неисправности. В остальном все тривиально: микроконтроллер в tqfp корпусе, 0805 рассыпуха, силовая часть выводная.
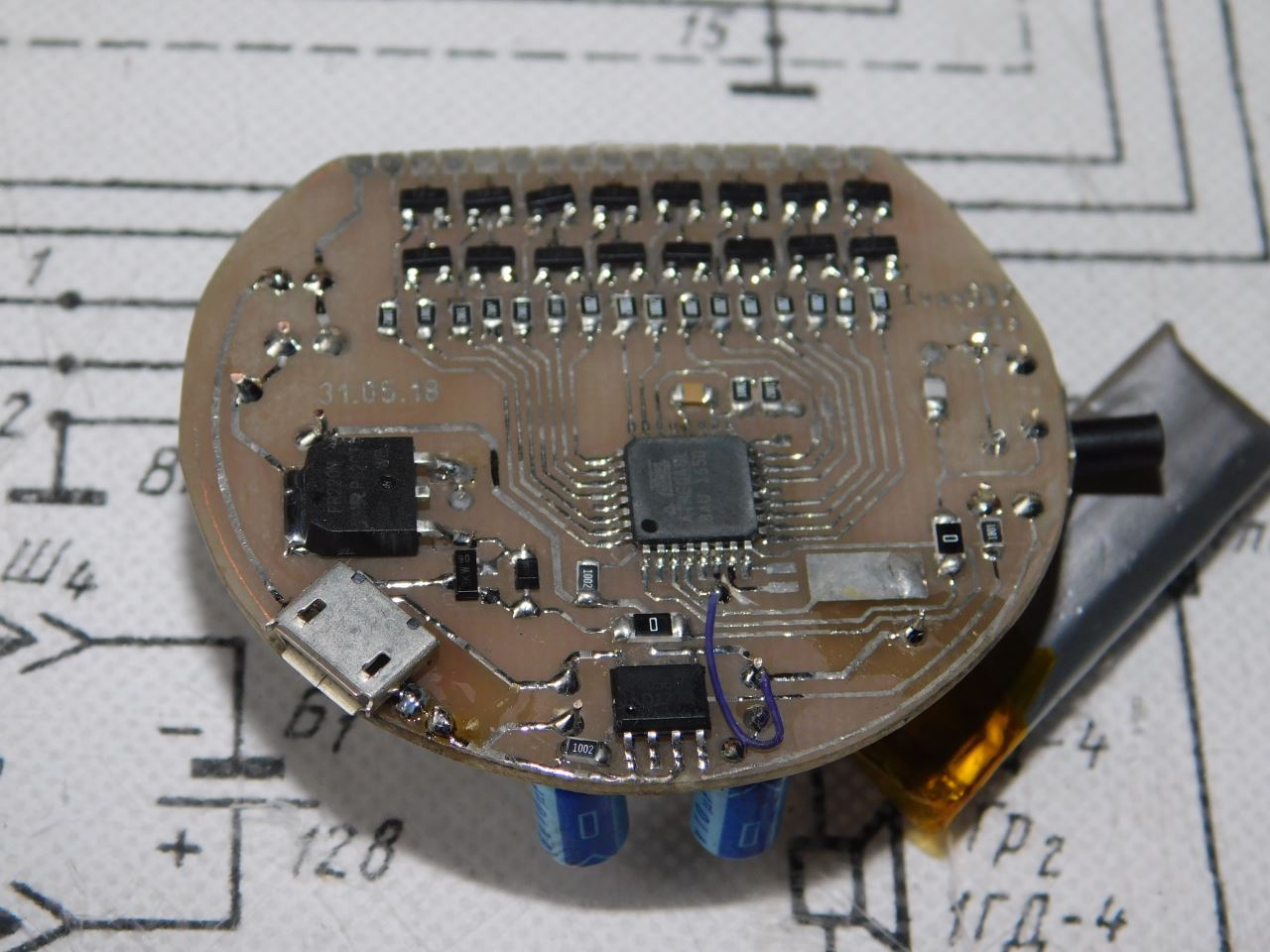
Изготовление корпуса
Итак, железная часть собрана, код для микроконтроллера написан, теперь необходимо сделать корпус. В моем случае я воспользовался 3D-печатью, так как у меня под боком две лаборатории с 3D-принтерами при полном отсутствии станков для металлообработки (есть только антикварные советские станки, на которых никто не умеет работать и они немного в раздестроенном состоянии). Мои часы полностью совместимы физически с часами Носова, и я взял уже готовую модель. На этот раз мне повезло с выбором принтера (количественно много, с качеством у них все плохо), и он напечатал довольно неплохо. Видимо, один из немногих грамотно настроенных.
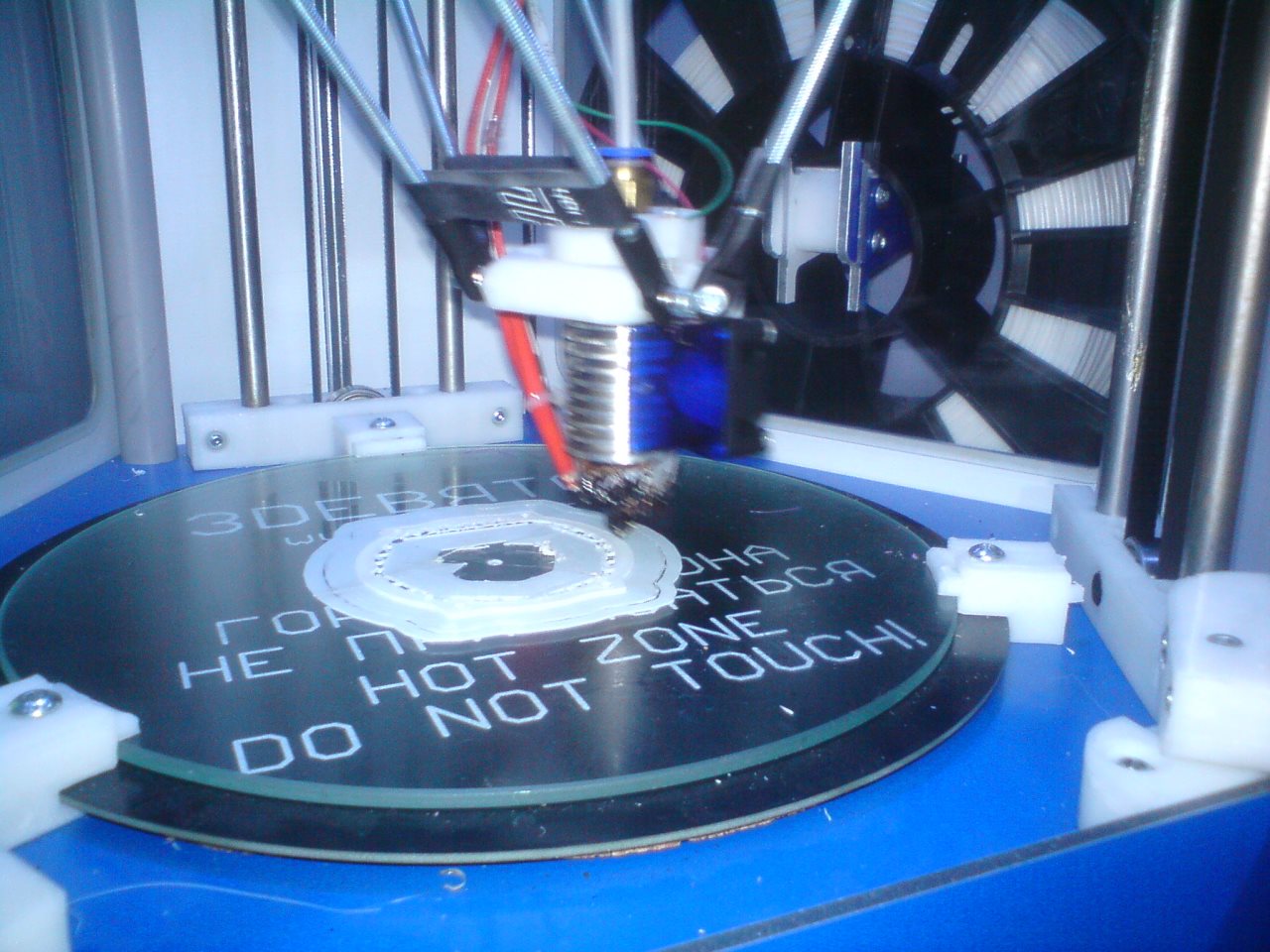
Если кто-то разбирается в принтерах, то обратит внимание, что этот 3D-принтер построен не по классической топологии, а является дельта-принтером. Печатающая голова летает по зоне за счет трех направляющих. У такого принтера сложная математическая часть, но в конце концов это сильно упрощает его конструкцию, но усложняет его настройку. Единственный плюс - небольшие габариты.
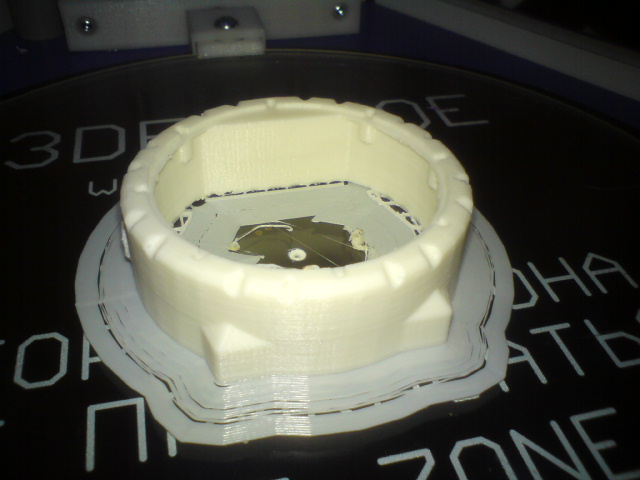
Без обработки напильником не обошлось, но сама модель получилась очень даже неплохо. К слову, модель в итоге я смоделировал свою, так как этот корпус был частично запорот в ацетоновой бане. Плату часов пришлось подгонять под корпус, в виду моей криворукости и невозможности ровно вручную разрезать стеклотекстолит по кругу. Так или иначе, все закрылось. Крышка снизу тоже напечатана.
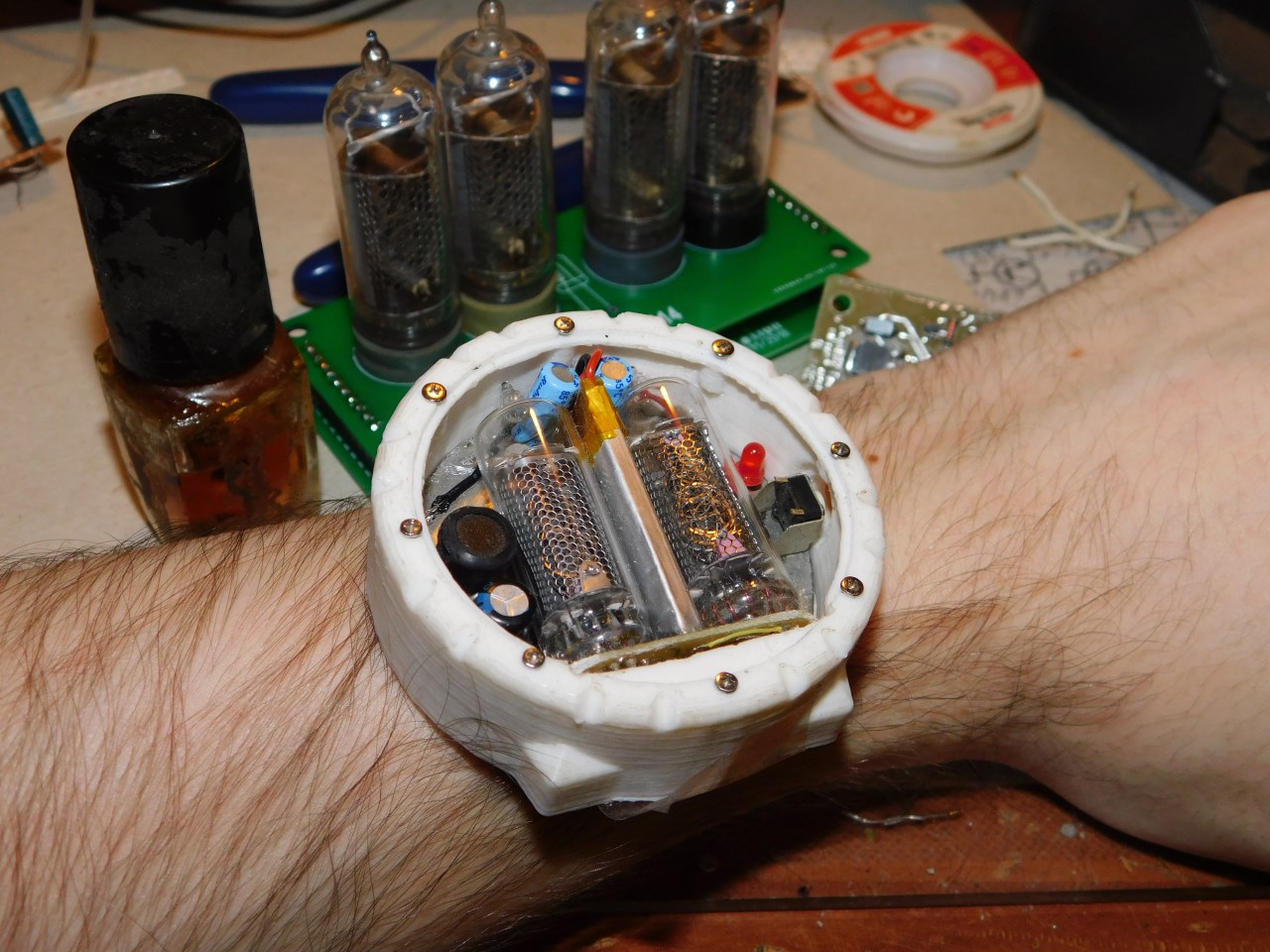
Стекло, винты и ремешок
Корпус рассчитан на стекло диаметром 50 мм и толщиной 1 мм. Был вариант вырезать такое самому из тонкого оргстекла, но этот вариант был отвергнут, по причине отсутствия солидности и сложности в вырезании. Под эти часы я купил стекло нужных размеров на Алиэкспресс. После небольшого уменьшения его диаметра на пару десяток и подрезании корпуса, стекло влезло. Конструкция оказалась немного нестабильной ввиду невероятной плотности компоновки. Лампы касаются стекла практически без зазора. Чтобы собрать все это безобразие, пришлось уменьшать толщину крышки и подтачивать немного выпирающий силовой транзистор.
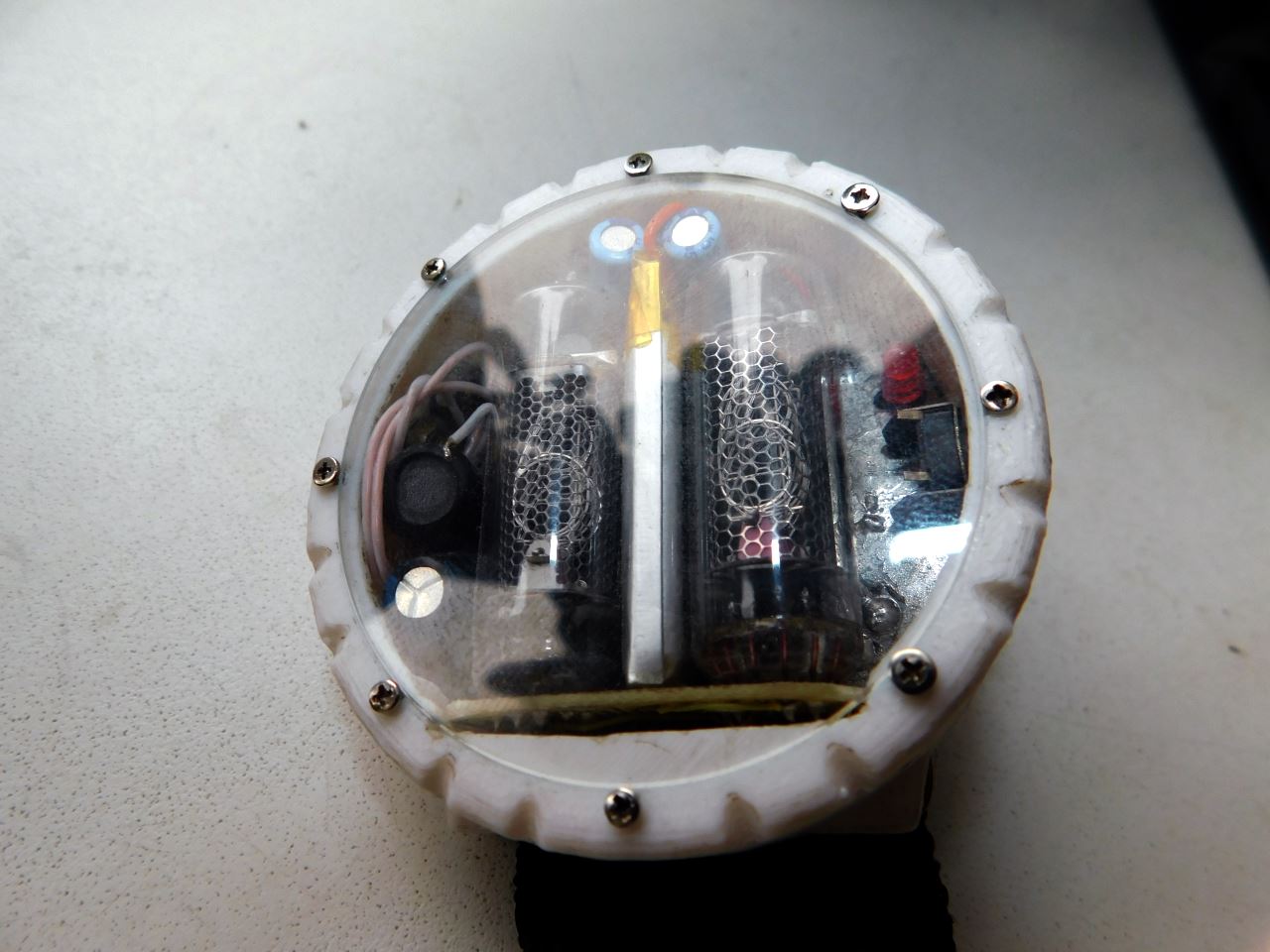
Винты я нашел случайные с разборок каких-то устройств. Когда при закручивании одного из винтов, по стеклу пошла трещина, я понял, что я делаю что-то не так... Как оказалось, из-за разных шляпок винтов, они оказывали разный прижим стекла к корпусу, что привело неравномерности распределения нагрузок в стекле и оно лопнуло. Немаловажную роль сыграла плотность компоновки стекла. Я заказал винты под шестигранник размерами 1,6х4 мм.
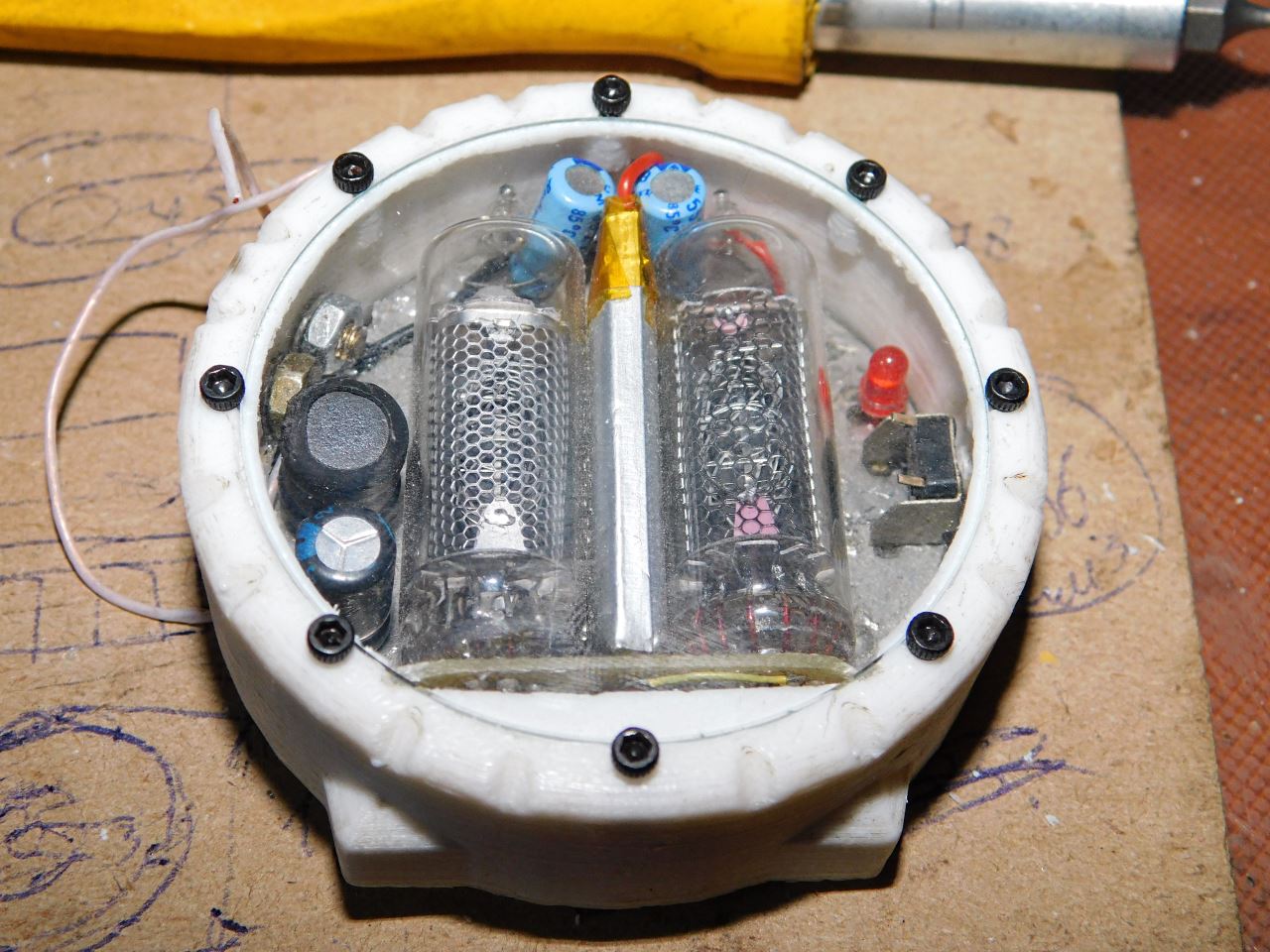
Новые винты все исправили и часы стали похожими на законченный продукт, не хватало некоторых мелочей. Ремешок был вырезан из длинного ремешка от какой-то сумки какого-то устройства. От того же ремешка была отпорота липучка, которая была проштопана на швейной машинке в нужное место. Крепления для ремешка вырезаны из листовой латуни. Латунь легко обрабатывается мелкими напильниками и также легко полируется.
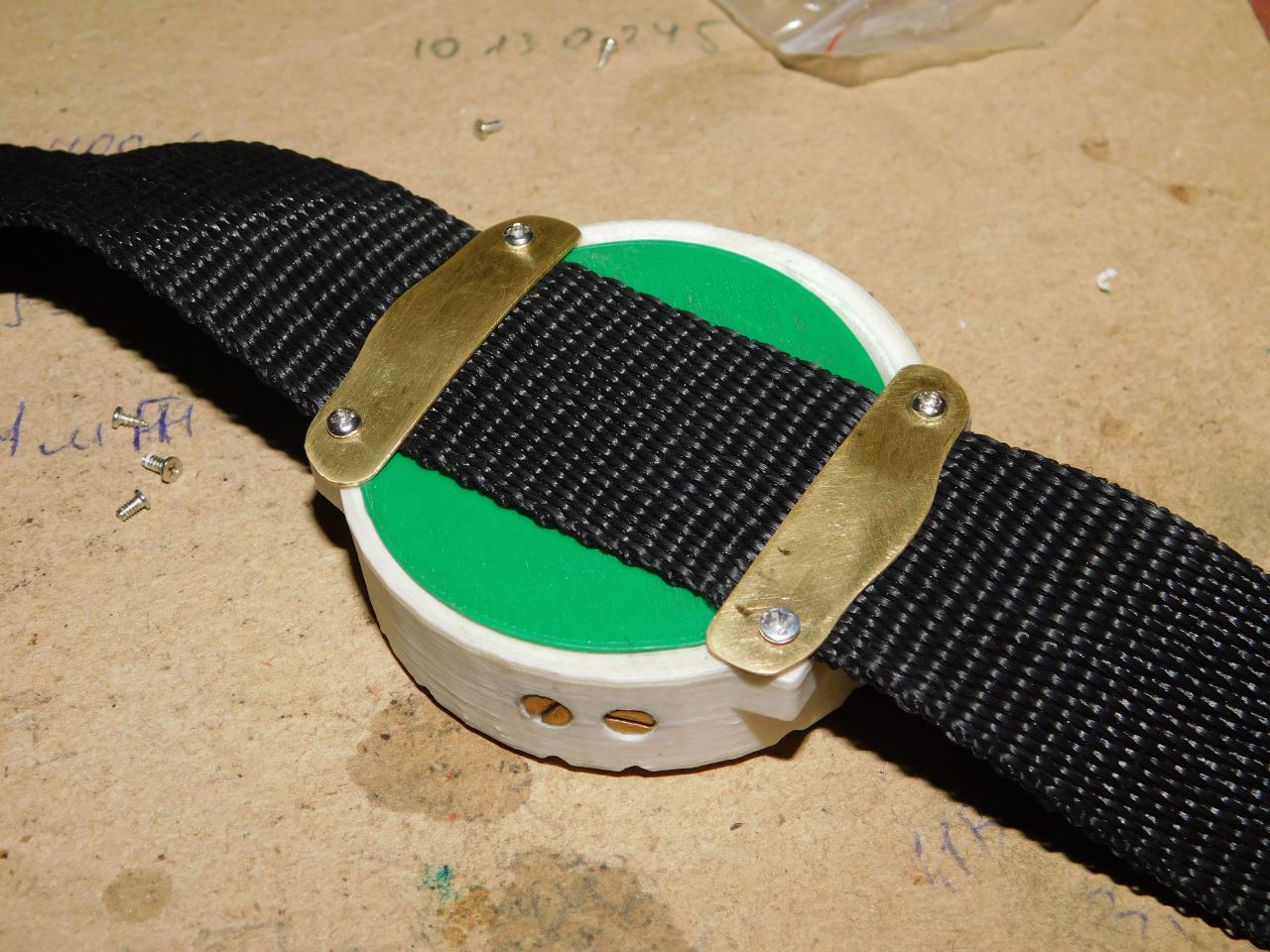
На этом фото видны два винтика на одной из сторон корпуса. Это - контакты для зарядки аккумулятора. С разъемом ничего не получилось, поэтому я выкрутился таким необычным способом. Часы вставляются в специальную станцию, в которой к ним прикручиваются два винтика, на которые подано напряжение.
Станция зарядки и о дельта-принтерах
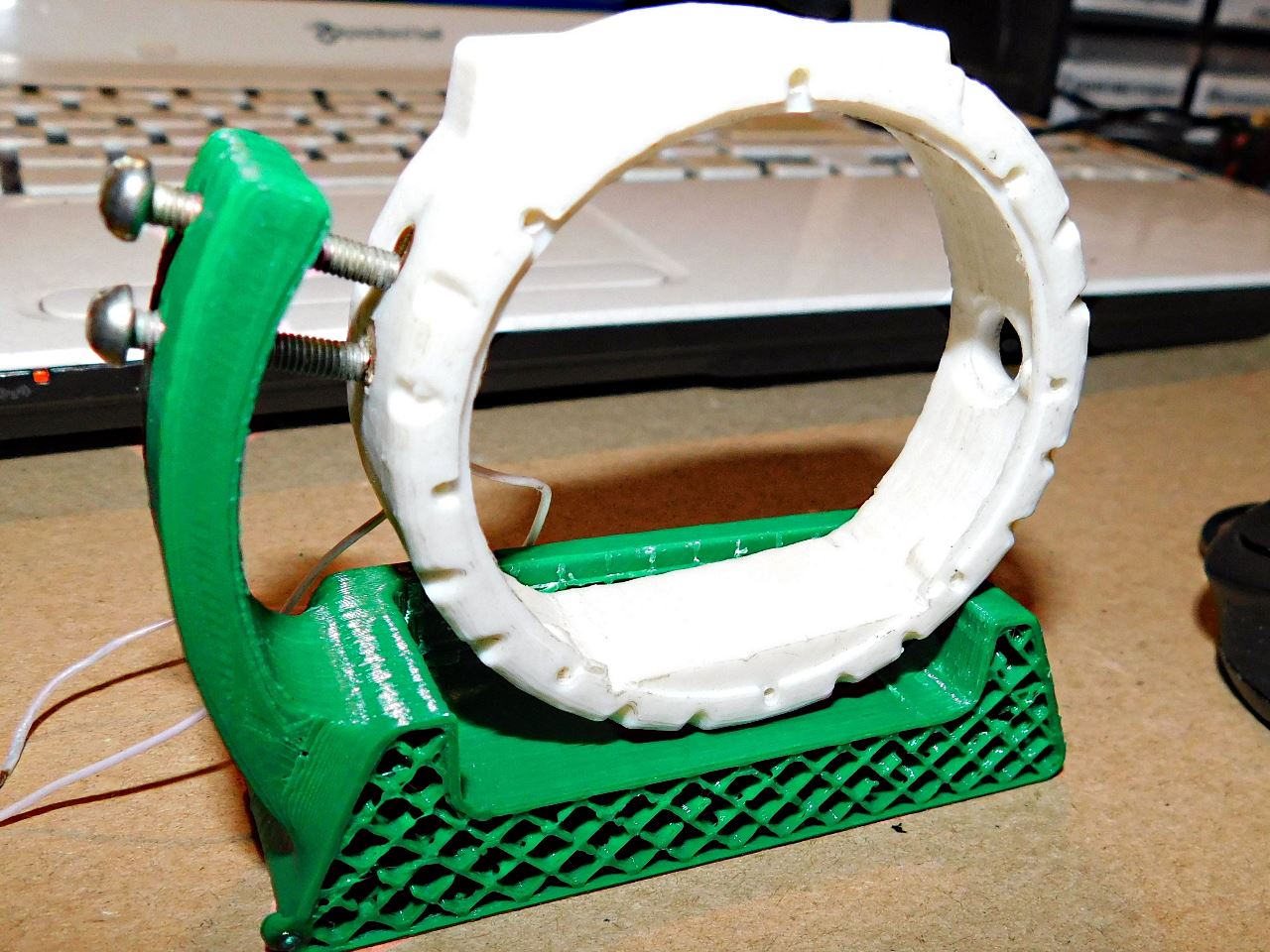
По неведомой изначально причине, 3D-принтер не смог закончить печать. После того, как он закончил несколько слоев, он начинает печатать по уже напечатанному. Происходит это из-за особенностей дельта принтеров. Дело в том, что оси Z в таком принтере как таковой то и нет, а движение вверх-вниз осуществляется синхронным движением сразу трех двигателей. И в результате перемещений не синхронных (вбок), сбивается в некотором роде координата высоты. Я думаю, в коде есть компенсация этого перемещения, но для аппаратной корректировки положения, в голове принтера предусмотрен датчик касания. Вот тут и начинаются проблемы...
Датчик представляет собой собственно крепление головки к тягам. Но экструдер не жестко закреплен, а подпружинен относительно крепления к тягам. Значит, когда головка касается стола или детали (горячей!) она немного отгибается (прощай жесткость), и там самым коммутирует два винтика, которые и представляют собой датчик касания. Конструкция мягко говоря не очень, по моим подозрениям все остальные 3D-принтеры поломали как раз по этой причине. Датчик ломается оттого, что проводки, подходящие к винтам просто прикручены на этот самый винт без всякой разгрузки или банальной трубочки. Рано или поздно оно расшатывается и принтер теряет датчик. К чему это приводит видно на фото.
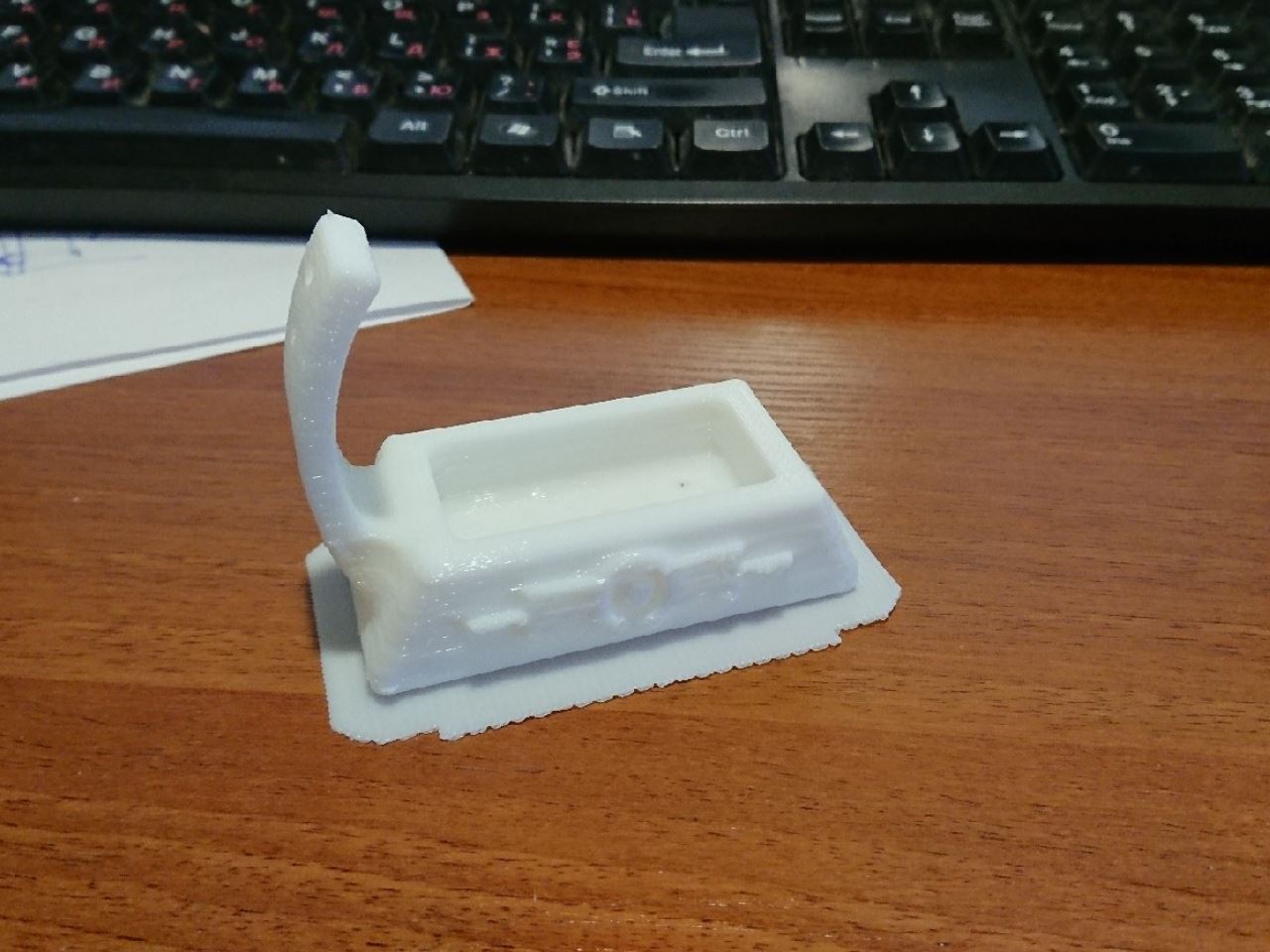
Станцию мне потом напечатал Артем Кашканов, поэтому эта проблема решена в некотором роде.
Облагораживание корпуса и ацетоновая баня
Часы почти закончены. Остались лишь доводочные операции: ацетоновая баня и покраска. Ацетоновая баня собирается из двух ведер (от мороженного и морской капусты), кипятильника на 500 ватт, сеточки для шпаклевки и ацетона.
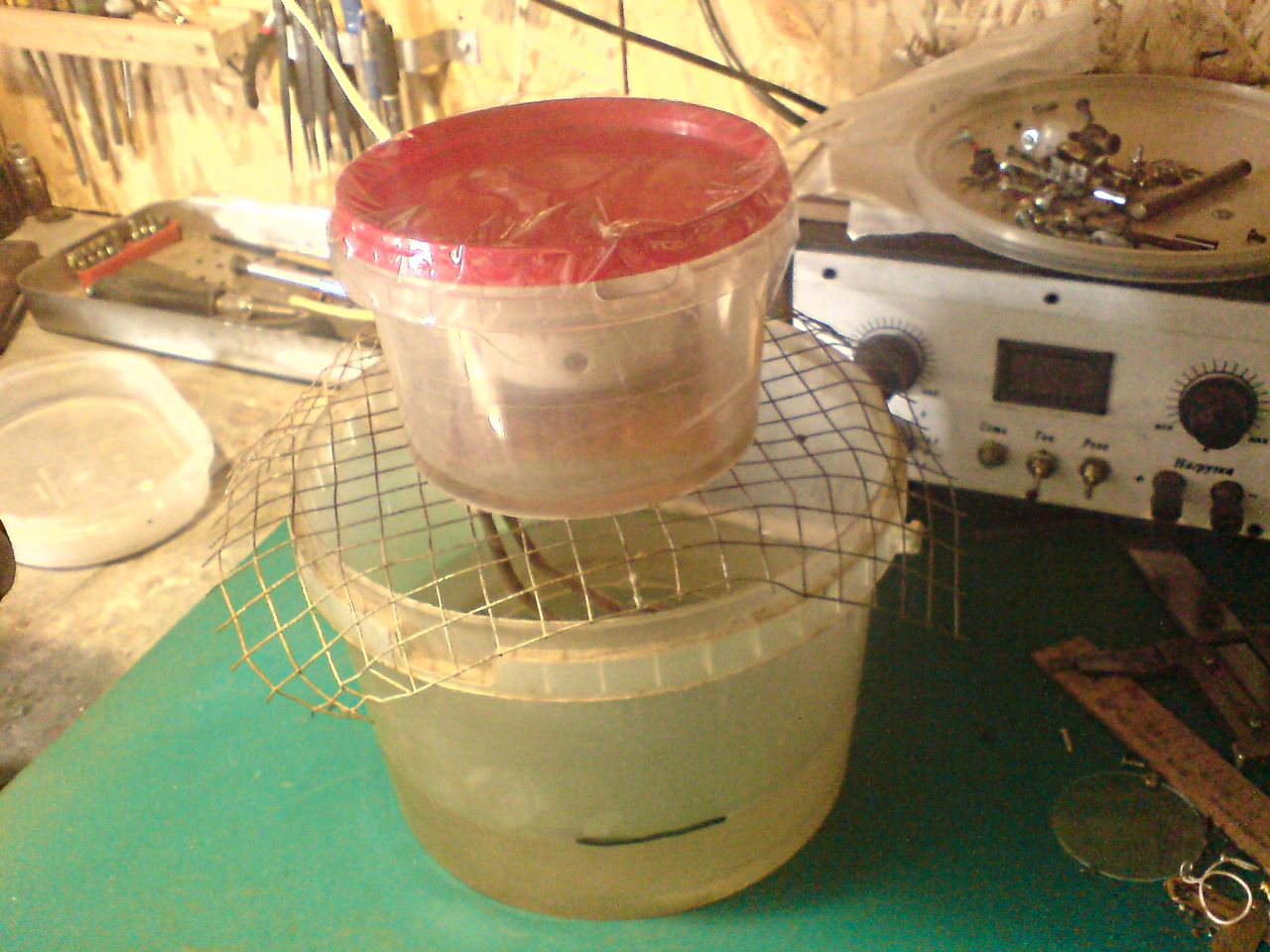
Суть ацетоновой бани - сглаживание корпуса с помощью плавления поверхностного слоя пластика. Так как модель напечатана классическим ABS пластиком, то его легко плавит обычный ацетон. Ацетон наливается в емкость тонким слоем, подвешивается модель и герметично закрывается для предотвращения выхода ацетона наружу.
Оплавляет модель не сам ацетон, а его пары. Поэтому, чтобы ускорить их появление, нужно нагреть ацетон чуть выше комнатной температуры. Нагревать прямо его нельзя (взрывоопасен), поэтому и нужна такая конструкция. Снизу вскипает вода и паром нагревает ацетон до необходимого состояния. Сильно нагревать не нужно.
Моя ошибка состояла в том, что я положил корпус на деревяшку в качестве подставки, но не учел, что она пропитается ацетоном и модель расплавит снизу. Это было фатальной ошибкой. Да, корпус получился очень гладкий и от слоев не осталось и следа. Первоначально, сразу после бани, модель еще мягкая и её нельзя трогать с каким бы то ни было усилием. Через некоторое время ацетон испарится и модель можно обрабатывать дальше. После часы были покрашены обычной аэрозольной эмалью черного цвета в несколько слоев.
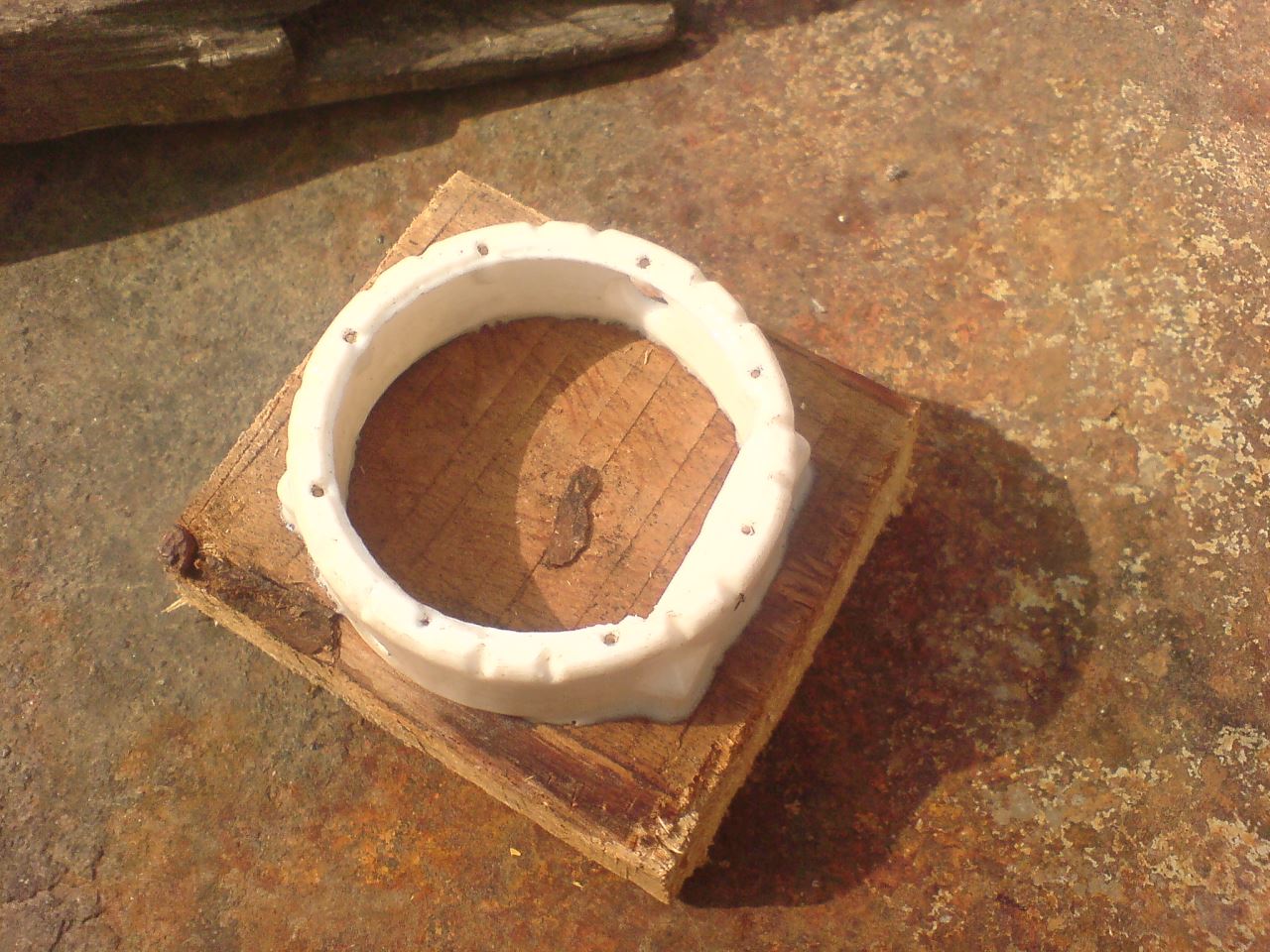
Конечная сборка и большой фейл
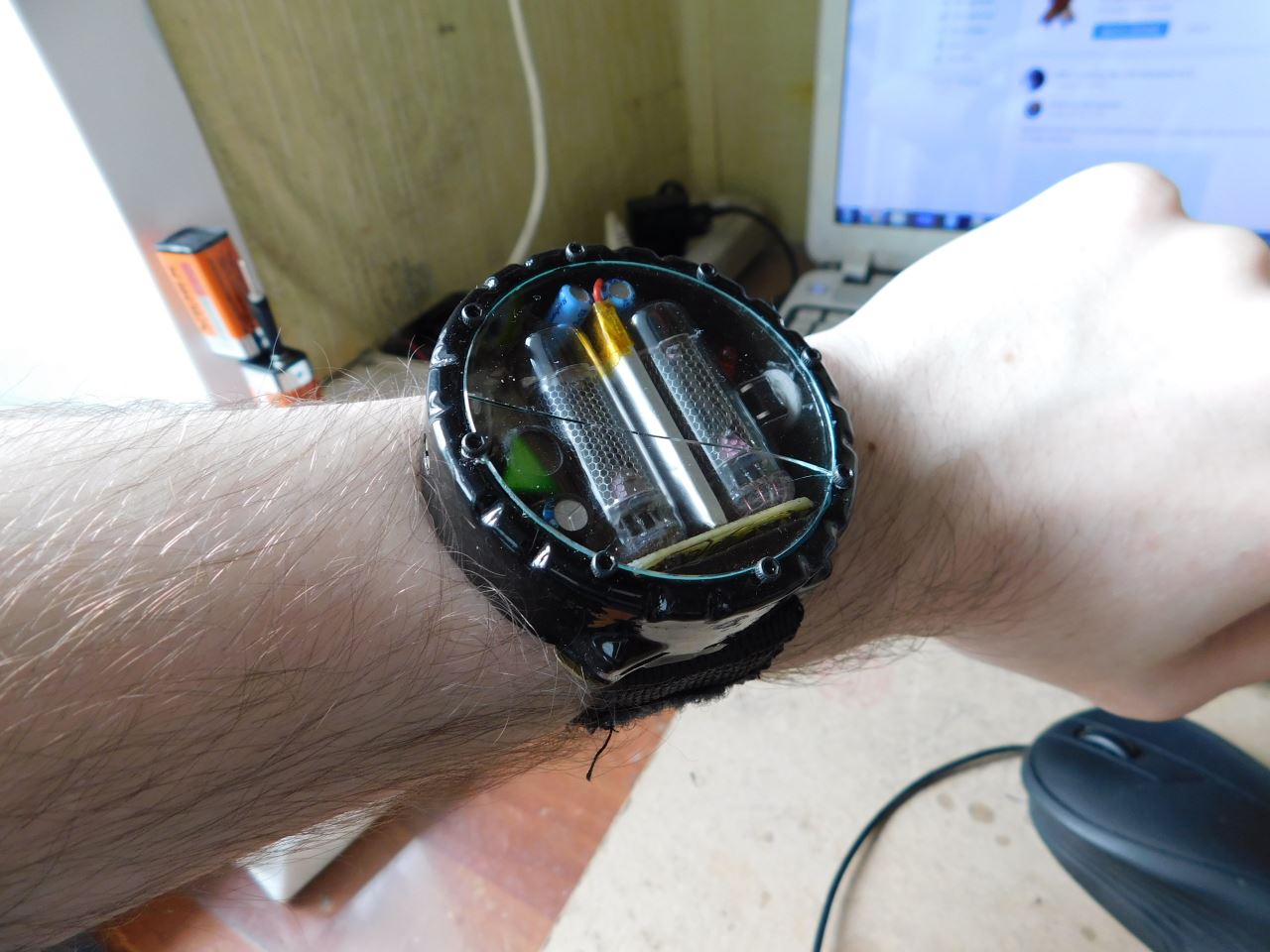
Мало того, что часы повело немного, так еще после трех слоев краски, все зазоры стали еще меньше, поэтому пришлось немного поработать ручным инструментом для решения этой проблемы. Днище расплавилось ровно на один миллиметр и пропал паз для крышки. Но это меньшая из зол - крышка закрывается ремешком и ее не так заметно. Из-за этого уплотнения часы еще сильнее стали давить на стекло... и оно лопнуло в один прекрасный момент. Оно, конечно, не раскололось на мелкие куски, просто прошла трещина. Тем не менее оно не выпало и, видимо, не собирается, поэтому его так и оставил.
В остальном, все в порядке, все встало на свои места. Да и трещина на стекле добавляет атмосферности и некоторой "брутальности". Напоследок немного технических подробностей: часы держат заряд при неспешном просмотре времени около 27 дней, что является неплохим результатом, но все таки не лучшим. Если бы я применил что-нибудь по-новее восьмой меги, то потребление в спящем режиме удалось бы снизить. Сейчас потребление во сне у часов около 220 микроАмпер, что многовато... Никакими способами мне не удалось уменьшить потребление, ну и ладно. Часы, конечно, крупноватые, но на руке держатся, хоть и немного спадают, тут уже виноват ремешок.
В целом, проект хоть и растянулся, но удался. Я доволен результатом, но все таки намерен переделать корпус под более серьезное стекло с антибликовым покрытием и в два раза большей толщиной. Новый корпус выйдет слегка выше, но кого это волнует...
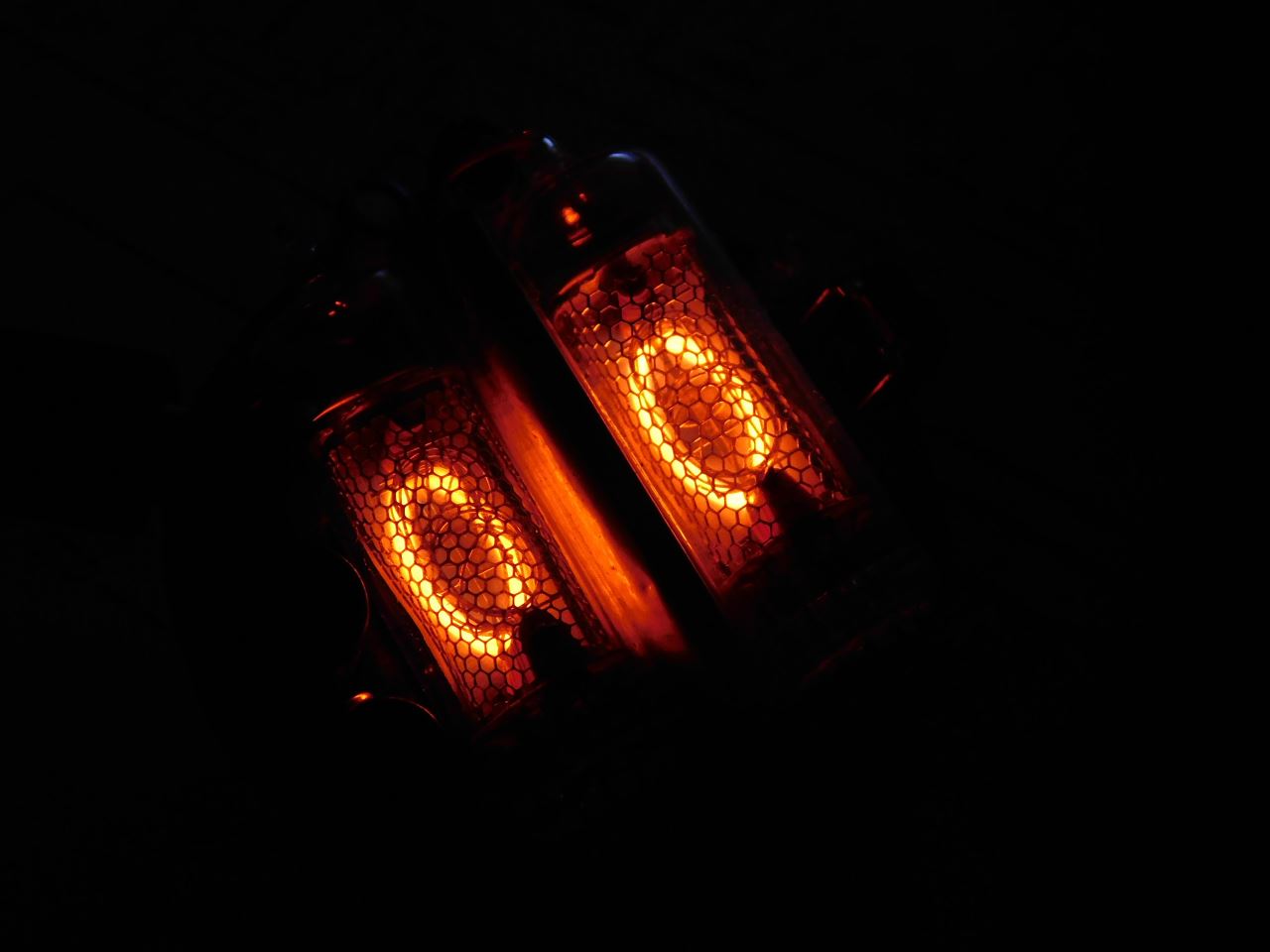
Домой - Статьи